Organic Brake pad (2): History and Development of Organic Brake Pads
Hello Steemit! been a while. I am writing this post as a sequel to my last post where I talked about the reason for Organic brake pads and the dangers of asbestos, in case you have not seen it, there you go - Organic Brake pads (1): Kicking out asbestos. Before I proceed, I'll like to appreciate everyone who dropped a comment on my last post (my first post on steemit actually), thank you all for your suggestions and encouragement. Today, we'll take a look at the history of brake pads and one of the ways by which they are made, so lets go.
HISTORY OF BRAKES
Brakes are essential parts of all means of transportation, we all need to stop at one point or the other so, whenever you need your bike, car, truck etc. to stop moving, then you need to call on the brakes - except you have mystic powers obviously.
For those that will like to know how brakes really work, I'll like to refer you to a wonderful post on how brakes work, failure causes and their preventions by @gtan.
Now, back to history, It is quite difficult to give kudos to a particular person or group of persons for the invention of brakes as there have been a lot of contributions, innovations and improvement to the optimization of stopping devices over the years. Come to think of it, those horses used as far back as the Roman empire era also had reins to make the horses stop. The first known vehicular brake however seems to be the wooden lever brake which involves the use of a brake lever that pressed a simple wooden block against the wheel in order to slow a cart down by friction. These however could only work on wooden carriages and steel-rimmed wheels and were very noisy.
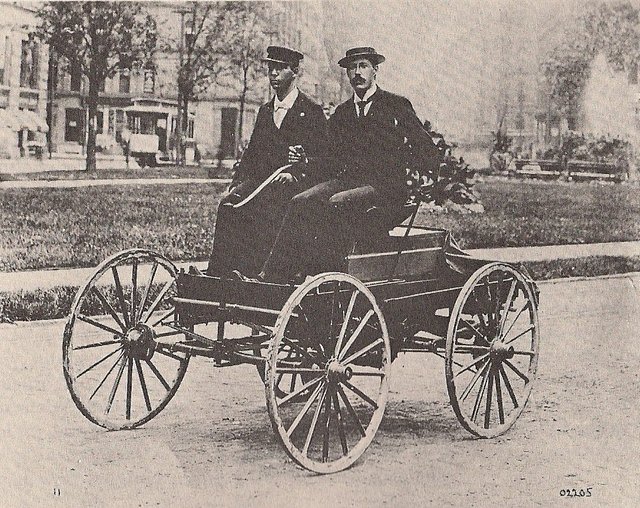
Image Source
Band brakes
The advent of the first set of automobiles saw vehicles which were just a little bit different from the previously used wagons and carriages but fitted with engines and drive trains which made them run a bit faster. This increased speed led to the invention of band brakes, as the name implies, the friction material was mounted around a hub on the wheel like a band and when the brake is applied, the friction material wraps around the hub, inhibiting motion.
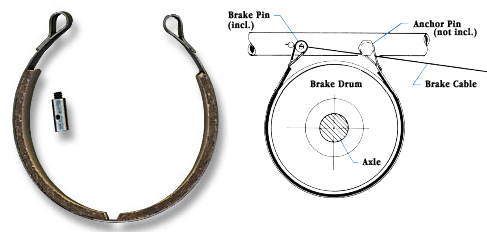
Image of the disc brake from aircraftspruce
What happened to band brakes?
Towards the end of the 1890s, the rim-contact braking system became obsolete due to the advent of rubber tires (Kudos to the Michelin brothers). The old system was no longer desirable as the band brake wears the tire very fast. This led to the brake pads being attached to the inside of the wheel leading to the first type of drum brakes. Just like the band brakes, the first set of drum brakes made use of mechanical linkages to provide braking contact for the brake shoe. Things however changed in 1918 when Malcolm Loughead proposed a concept of a four-wheel brake system using hydraulics. I bet the man sat down and thought about fluids and their incompressibility and decided they could be of good use, whatever the case may be, it turned out well and hydraulics is the basis of braking systems in automobile right now.
Drum brakes
These types of brakes have the friction material attached to the inside of the hub. The hydraulics assisted drum brakes make use of fluids to actuate the piston(s) located in the assembly. This piston pushes against the friction material often referred to as the brake shoe and the brake shoe bears against the rotating hub, thereby slowing down or stopping the vehicle. These types of brakes were good because they were enclosed and this enclosure keeps dust, mud and other elements out of the system. However, due to the fact that they are enclosed and the surface area in contact at any point in time is large, they cannot handle higher heat dissipation rate needed when large vehicles and very fast vehicles are brought to a stop.
What happened to drum brakes?
The disc brake is widely accepted to be more efficient than the drum brake and is widely used in different types of automobile. This can be attributed to the fact that as the automobile industry boomed, more improvements were made on cars and their engines and vehicles became larger resulting to more workload for the brakes. This increased workload could not be borne by the drum brakes as there was a need for high heat dissipation rate which the drum brakes could not provide. For this reason, some recent cars employ the use of disc brakes on all wheels while the use of drum brakes on the four wheels of a vehicle can only be found in very old models. In some models however, you will notice that the rear wheels have drum brakes while disc brakes are found in the front wheels of the vehicles, this is because the front brakes play a greater part in stopping the car than the rear ones. Try and remember what happens when a car brakes (especially when the driver brakes hard), you notice that the passengers are thrown forward and the car also tend to "lean" forward. This happens because braking action throws the weight of the car forward on to the front wheels as there is a forward transfer of weight due to inertia.
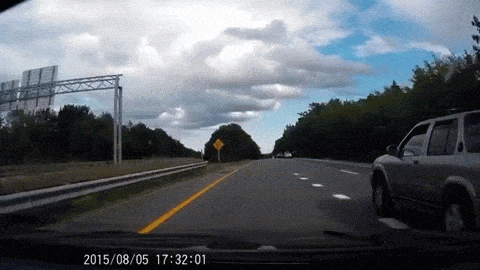
Giphy
Disk brakes
It is surprising to know that the disk brake was patented as far back as 1902! Yes, it was invented before the drum brakes but was neglected due to its screeching noise and large effort requirement while braking as it has not been incorporated into a hydraulic system. If you have ever ridden a bicycle then you should understand the concept of the disc brakes as that is the principle of bicycle brakes. When the brake lever on the handle bar is pulled, a thin metal cable which runs from the lever to the wheel pull on small calipers, forcing thick rubber blocks to press against the wheels. This system works well with bicycles as they are smaller compared to cars. In 1907, Herbert Frood however solved the noise problem by lining the pads with asbestos which braked quietly and lasts long.
Disk brakes were however brought back to limelight when Chrysler incorporated a hydraulic system into it and released its imperial cars working on hydraulics-assisted disc brakes. The asbestos brake pads then became widely accepted till around 1980 when the quest for organic brake pads began due to reasons stated in my last post Organic Brake pads (1): Kicking out asbestos
BRAKE PADS
A brake pad can be referred to as a substance that acts as a friction lining material in disk brake assembly (for bicycles, it is the thick rubber blocks)
Image source
Categories of brake pad constituents
Brake pad can be classified into two main categories; According to the matrix material and According to material source
1 According to matrix material
According to the matrix material, brake’s friction materials can be divided into metallic, semi-metallic, and non-metallic matrix;
Metallic matrix: These composite materials contain a minimum of two constituent parts which should include a metal and another material, or two different metals. One of the constituents is reinforced with the other material in terms of strength with the aim of improving its tribological properties. After a homogeneous mixture with other friction additives is made, these metal powders are then pressed to form powder metallurgy friction material.
Semi-metallic matrix: The principal components of semi-metallic matrix friction material are metal fibre, ceramic fibre, and copper or iron powder. Semi-metallic matrix friction material has great heat resistance, high power absorption, and excellent tribological properties. However, it also has some shortcomings such as low-frequency noise, easy rusting, and serious damage to brake disk. Presently, semi-metallic matrix friction material is widely applied in automobiles, motorcycles and other light vehicles.
Non-metallic matrix: This refers to a friction material matrix which does not have metal as part of its constituents. Here, modified resins like phenolic, epoxy and rubber are used as a binder, while organic fibres such as kevlar, carbon etc. or inorganic mineral materials like glass and wollastonite are used as reinforcing fibres. They are solidified by hot pressing after uniformly mixed with other friction additives. They are used widely because of their lower cost and also because they provide higher strength to weight ratio
2 According to material source
There are two main kinds of classification according to material source, the powder metallurgy friction material and the organic friction materials;
Powder metallurgy friction materials: It consists essentially of a continuous metal matrix, into which varying amounts of non-metallic friction generators, such as silica and emery are bonded.
Organic friction materials: It is most widely used due to its simple preparation method, excellent tribological properties and eco-friendliness. Generally, organic friction material consists of binder, reinforced fibres, friction additives, and fillers
Organic brake pad development
As is the case with most engineering practice, material selection is always one of the first steps of this kind of production. For organic brake pads, there are four main categories of constituents from which suitable choices must be made with due considerations given to cost, availability and processability. Below are the four main constituent categories and their importance
i) Fillers: The fillers are used to improve the process-ability and reduce the cost of friction material. Generally, organic or inorganic fillers can be used. They include; vermiculite, mica, and barium sulphate, jute, glass fibre, kenaf etc. In this case, however, an organic material is necessary. This should be kept below 55% since it is from an organic source and it makes the composition more susceptible to high porosity, wear and low flame resistance. Choice materials in this category should be materials abundant in nature or agricultural wastes such as maize husk, bagasse etc.
ii) Reinforcing fibres: The reinforcing fibres are used to improve friction performance and mechanical strength. The metal fibres (iron, copper, etc.), glass fibres, carbon fibres, and organic fibres such as kevlar, cotton, ceramics are used as reinforcing fibres. This is should be kept below 15% as it usually doubles up as an abrasive even though it is meant to improve the mechanical strength of the composition.
iii) Friction additives: They determine the frictional properties of brake pads and comprise a mixture of abrasives. The friction additives can adjust friction properties and control wear behaviors of brake’s friction materials. Generally, the additives can be classified into two types: lubricant and abrasive. The lubricant is always used to reduce the wear of friction material and is advisable to be between 4-10% of the composition. If it is too little, the composition might be too abrasive and might destroy the rotor disc of the car while the brake will lose effectiveness if the lubrication is too much. For example, as an excellent lubricant, graphite can decrease wear rate effectively by reducing the direct contact between surface of friction material and brake disk. The abrasive (e.g. metal sulphide) on the other hand is generally used to increase friction coefficient and strengthen wear resistance of friction material. This constituent should be kept between 5% and 27% and made to vary as the filler is being varied since the abrasive and the filler are meant to complement each other for improved process-ability, reduced cost and a controlled abrasiveness so as to prevent damage to the rotor disc.
iv) Binder: Binders are responsible for holding all the constituents of a brake pad together and prevents them from disintegrating. They reduce the cost and improve the manufacturability of brake pads. Examples include Phenolic resin, COPNA resin, Silicone-modified resin (Phenolic siloxane resins), Epoxy-modified resin, Cyanate ester resin and thermostatic Polyamide resin. The percentage of the binder is usually determined by a trial by error method. After the quantity of other constituents have been fixed, a trial mix is made by adding the binder till the mix forms a dry paste (be careful not make the paste too moist or slurry). The amount of binder used to form the paste is then noted and will be used throughout the experiment.
It should be noted that certain substances can perform more than one function and therefore can be placed in more than one category.
Developing a new composition
When developing a new organic brake pad composition, a research is carried out which investigates not only the different compositions created but different particle sizes of the filler as this can have a great effect on the property of the produced sample. Different sample compositions can be made by varying the percentage of the filler and that of the complementing abrasive. After a number of sample compositions have been developed, different particle sizes for each sample can also be investigated. As I said in the part one of this sequel, I also developed my own brake pad using elephant grass as a filler. In my own research, I created 5 different sample compositions and investigated 3 different particle sizes for each sample.
Each composition is the mixed properly, transferred into the mould to be used (which must have been previously oiled) and compressed. A hydraulic press is suitable but a manual press will do the work just fine. The produced sample is removed from the mould and placed in an oven, heated at 150°C to cure. In the absence of an oven, the samples can be placed in a dry tray and left to cure for 48hrs before the necessary tests are carried out on them. These tests are meant to compare the mechanical and tribological properties of the produced samples with that of the commercially available brakepads so as to determine their acceptability.
So far, I have mentioned how braking moved from the "primitive" wooden wedge to the present hydraulic brakes. It is worthy of note that some systems and devices like the ABS (Anti-lock Braking System) and EBD (Electronic Brakeforce Distribution) are now incorporated into modern day braking to improve safety and increasing braking efficiency. You might want to go through this short but explanatory video on ABS posted by @showroomcar some months ago. The later part of my post then exposed the categories of constituents that can be found in a typical organic brake pad and how new formulations can be developed. Looks like it is not that difficult, or is it?
This is the second part of the Organic brake pad series, I hope you like it. Stay tuned for the third part where I'll share how I produced an organic brake pad from Elephant grass, my experience and challenges. Thank you
- mentalitch
- Autoevolution
- Greg Monfonton and partners
- Aaron, G. (2017). Disc brakes vs. Drum brakes: How they work and which is better web blog post
- Holifield, P., & Weil, N. (2009). Materials of Brake Pads . PowerPoint slides
- Majethia, K. (2017). Non-metallic and composite material. web blog post
- Mutlu, I. (2009). Investigation of Tribological Properties of Brake Pads by Using Rice Straw and Rice Husk Dust. Journal of Applied Sciences, 9, 377-381. DOI: 10.3923/jas.377.381
Wonderful post well articulated. Regardless of their small sizes, they are invaluable in automobile braking systems
Brake pads are truly life savers and these are little things we do know that affects our lives so much.
Good job Michael, I like your post.
Thank you
@mykelade, this is a awesome write up, taking us through the history of brake pads and even more. Kudos!
Also, please try to break large blocks of text into smaller ones to ease reading. By the way it becomes more appealing.
Thank you. I'll work on that
You are welcome.
Brake pads are consumables that are vital to the braking system. Just like brake fluid, they are often overlooked, and the consequences can be disastrous.
Kudos bro...nice read!
Thank you
👍
The organic brake pads are very much new.. I haven't read much about then till now.. Well done.
Thank you