THE AIRCRAFT: DESIGN, MANUFACTURING AND MAINTENANCE
Making reliable aircraft:
That airplanes transport us safely is not only the responsibility of the pilots, or the technicians who are responsible for maintenance and repairs, or air traffic controllers, but is due to the interrelation that exists between the many areas involved in the security chain that supports air transport.
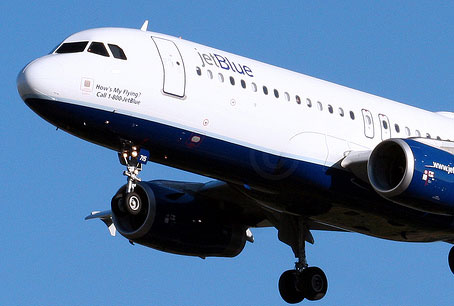
The current scenario of commercial aircraft manufacturers presents, due to the important high technology entry barrier that there is a situation of competition between two major manufacturers: the European Airbus consortium and the American company Boeing. There are many other construction companies, but their level of technology or production is far behind them.
But apart from the commercial competition that exists between these manufacturers, logically on the other hand, both share a common interest in their respective strategies to focus their research, design and manufacturing activities on ensuring the maximum reliability of their aircraft, since it the security they provide during their operational life will depend.
I do not exaggerate if I affirm, that no other industry related to transport is subject to such exhaustive processes for its design, manufacture and maintenance as the industry related to air transport, which does not prevent, from time to time, failures occur , some even unsuspected.
Design considerations:
When a manufacturer decides to start the production of a new airplane model, together with the opinion of the airlines about their needs, analyze the evolution of the price of fuel, environmental restrictions imposed by noise and other problems associated with the environment environment -without forgetting any improvement that the competition had introduced in its airplanes-, improvements are added that make the plane safer.
The airplanes are designed and built to be able to overcome complicated situations, both from the point of view of maneuvers proper to the flight, and against adverse weather. Up to a certain limit, of course. You also have to rely on the expertise of the pilots.
During the design phase, the first conditioning factor is security. Hence, the commitment is to ensure that the probability of a single failure having catastrophic effects for the aircraft is one in a billion, that is, extremely remote. In this way, it is practically guaranteed that such a situation should not appear in the entire operational life of an airplane model, 25 or 30 years, and even more. In any case, that this is the objective does not mean that it is actually fulfilled.
The pillars on which the reliability of an airplane is based are:
The redundancy of critical systems
The robustness of the structure, as well as its resistance to the effects of fatigue of materials and tolerance to external damages.
The reliability of operation of the systems.
The effectiveness of warning and anomaly detection systems.
The establishment of scheduled maintenance intervals, which guarantees the timely detection of any problem.
The continuous improvement during the years that the manufacture of each airplane model lasts.
Thanks to this systematic way of working the current aircraft are very reliable. Hence, the meteoric evolution experienced by the air transport industry.
The pilots' cabin:
One of the priorities in aircraft design focuses on the cockpit of the pilots and the interaction of these with the instruments and flight controls, which is known as ergonomics. It is the man-machine relationship.
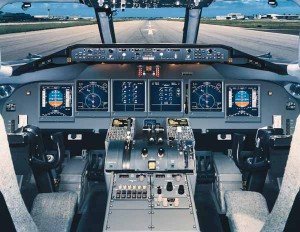
In this regard, the development of computers, specific computer programs and video monitors has made it possible to replace traditional analogue instruments with multifunction displays and increase the reliability of the systems, thereby improving the management of information in the booth.
Following the principle of redundancy, each aircraft is currently designed so that, in case any of its equipment and systems fail, another assumes its functions. Thus, flight instruments such as speed and altitude indicators, the artificial horizon, communication systems and others, are even found in triplicate in the pilot's cabin. In addition, among other improvements carried out, numerous lighting and acoustic warnings have been replaced by synthetic voices -generally in English-, which call the attention of the crew to the incidents that take place.
The structure of the plane:
En la actualidad, el concepto clave en el diseño y fabricación de aviones es la reducción de peso. Gracias al aluminio y a su aleación con otro metal aún más ligero como el magnesio y a los materiales compuestos como la fibra de carbono, ha sido posible aumentar el tamaño de los aviones sin comprometer su peso. Dos buenos ejemplos son el Boeing 787 y el Airbus 380, aviones que cuentan con una elevada cantidad de piezas fabricadas con materiales compuestos.
Con este tipo de materiales ligeros y resistentes se consigue aumentar la resistencia estructural del avión al tiempo que se reduce su peso, lo que se traduce a nivel operativo en menor longitud de pista necesaria para despegar o aterrizar, menor consumo de combustible y menor ruido generado por sus motores.
Por otra parte, esta reducción en el peso también ha hecho posible triplicar y cuadruplicar muchos sistemas importantes y, con ello, reducir la probabilidad de un fallo total de sistemas críticos. De ese modo, los fallos simples, e incluso dobles, no deberían causar incidencia reseñable en cuanto a la seguridad de vuelo.
Con independencia de los materiales que se utilicen, la estructura de un avión debe diseñarse para soportar ciertas cargas máximas. Las alas, por ejemplo, deben soportar cargas de aproximadamente 3g -tres veces el peso del avión [16]– y cargas de rotura de 4,5g, límite hasta el que no se permiten deformaciones estructurales ni roturas.
Estas cargas máximas de diseño se espera que ocurran, como mucho, una vez durante la vida operativa del avión, mientras que las cargas menores debidas a volar en turbulencia y ejecución de maniobras de vuelo pueden producirse miles de veces.
En vuelo, son las alas las que aguantan todo el peso del avión, por lo que tienden a curvarse hacia arriba por un efecto combinado del peso y la sustentación -véase la foto-. Lo contrario sucede cuando el avión está en tierra: las alas sólo soportan su propio peso -y el combustible que albergan sus depósitos-, por lo que se suelen doblar muy ligeramente hacia abajo. En el caso del Airbus 380, cuyo peso al despegue es de unos 500.000 kilos, estaríamos hablando de 2,5 millones de kilos que deben soportar las alas sin deformarse permanentemente, ni romperse.
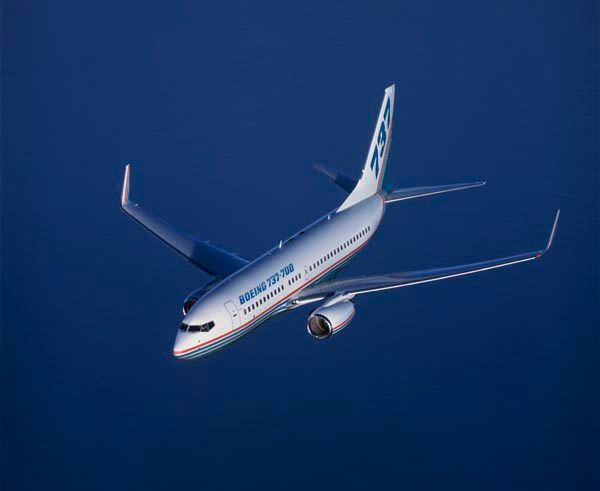
In addition, the airplane's own structure must also be able to withstand a large number of load variations throughout its operational life. For example, the horizontal stabilizer of the Boeing 787 is capable of supporting 150% of the maximum aerodynamic load it can find in flight. These load variations that occur when taking off and landing, maneuvering and flying in turbulence, cause tiny cracks that, if allowed to grow beyond the calculated tolerances, can cause structural failure due to fatigue of the material, even with the application of loads much lower than the maximum calculated during the design process. What it takes, that by system the maintenance manual of the airplane mark blocks of flight hours after which it is necessary to make an exhaustive examination of the structure, question this is addressed in chapter 8.
Aluminum, key in the construction of modern aircraft:
A combination of lightness, resistance and high electrical and thermal conductivity, is the property that made aluminum and its alloys a key material for the construction of aircraft, cars, or internal combustion engines, among many other applications. And is that a given volume of aluminum weighs less than a third of the same volume of steel. The only lighter metals are lithium, beryllium and magnesium.
On the other hand, it only presents 63% of the electrical conductivity of copper for wires of the same thickness, but weighing less than half. This means that an aluminum wire of conductivity comparable to a copper wire is thicker, but still lighter. All this is important in the case of the transport of high voltage electricity -700,000 volts or more- it lengthens the distance for what, precisely, aluminum conductors are used.
The landing gear:
It is one of the most critical elements of the design of an airplane, since it must withstand very strong impacts during landing. In addition, to brake safely, carbon disc brakes and anti-lock wheel systems -ABS- were developed and later exported to the vehicles we drive, and even to the railroad. On the other hand, instead of using very large wheels to support large weights, we choose legs with several axles and multiple tires called boggies, which allows us to distribute the weight better between all the wheels and avoid incidents in case of a puncture or blowout of any of your tires.
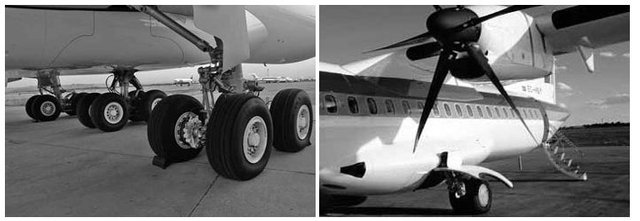.jpg/)
The engines:
A fact that designers take into account when choosing the engines for a new model, is the total weight that the plane will have at the moment of takeoff-own weight + passengers + cargo + fuel-, since these must be able to generate, at least, a force - tons of thrust - equivalent between a third and a quarter of the total weight of the airplane to get it moving, accelerate, counteract the resistance to the advance of the air and reach enough speed for the wings to generate the necessary lift to take off. For example, in a commercial airplane with a capacity of 100 passengers and 50 tons of weight, each of its two engines needs to generate eight tons of force. While in the case of the A380, each of its four engines has to generate about 35,000 kilos of thrust x 4 = 140,000 kilos to move an approximate weight of 560,000 kilos, a quarter of the weight.
On the other hand, without the development and evolution that the jet engine has experienced, the advance of air transport itself would not have been possible. An example is found in the DC-3 piston engine, which needed a review every 500 hours of flight, while the engine of a Boeing 767 should be reviewed every 30,000, which gives an idea of the reliability of one and the other. Reliability that is due, among other things, to the fact that the materials with which it is built can withstand thousands of hours of operation at enormous temperatures without deteriorating.
Another aspect that has also evolved has been the increase in its diameter, the immediate consequence of which is a drastic reduction in the noise generated due to the reduction in the speed of the exhaust gases.
We are all surprised by the apparent ease with which large commercial airplanes gain speed on the runway and, in less than a minute, raise their several hundred tons in the air. In those moments, each one of the engines, for example of a Boeing 747, develops a thrust of almost 30 tons. Push, whose greater part of the effort is supported by the great rotor of almost three meters of diameter that is appreciated when observing the engine in front. It is known as a fan-fan.
The development and production of these engines is a very specialized task on the part of the manufacturing companies. The competition is tough and all aim to design the most efficient engine that provides the greatest thrust with minimum fuel consumption, as this decisively affects the operating costs of airlines. The key aspect is the development of materials more resistant to stress and fatigue, lighter and that tolerate high temperatures without losing their qualities. A turbofan engine, such as the one developed for the Airbus A380, absorbs 1.2 tons of air in every second during its flight operation thanks to the fan. 87% of this air is driven directly backward, as would a propeller, while the remaining 13% is compressed and mixed with the fuel to produce, after passing through several stages, enough energy to move at high speed the fan.
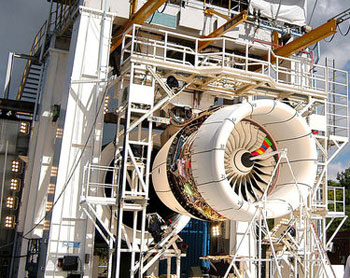
And the greater the diameter of the fan, the compression ratio of the air and the temperature in the combustion chamber, the more efficient the engine will be. The problem is to have materials that resist these efforts and temperatures.
The fans are made of a titanium alloy. Their blades are not solid, but hollow and stuffed by a lattice of supports like honeycomb. It is striking that they are of one piece, without rivets or welds, and that they are attached to the central disc also without welding. The reason is due to a physical property of certain alloys known as superplastics.
Superplasticity is a curious phenomenon that occurs even in the hardest and most resistant alloys known. Take for example titanium, a light metal but very hard and resistant even at very high temperatures. However, alloying it with 6% aluminum and 4% vanadium becomes extremely ductile between 900 and 950 degrees Celsius, well below its 1,600 degree melting point. Temperature fork in which the alloy is left to mold as if it were plastic. Without losing its hardness, the alloy can be stretched to more than fifteen times the original size and different pieces can be joined by simple pressure.
The scientific explanation of this curious property is not simple, because it is born from the complex dynamics of the atoms that make up the alloy. At present, half of an airplane engine is made up of superplastic alloys, and the tendency is to build it entirely with this type of material. A curiosity, which I thought it appropriate to tell you in case you want to show off to your friends.
- From manufacturing to flight online:
All aeronautical aircraft, parts and equipment that are manufactured in the member countries of the European Union, must be built according to the same technical standards, and validated following a single certification system defined by the European Aviation Safety Agency, EASA. In this way, homogeneity is guaranteed in all aircraft manufactured in Europe. There are just over two dozen countries whose industry has the capacity to design and manufacture aircraft. The rest, usually recognizes the type certificates [17] issued by the North American aeronautical authority -FAA- and the European Aviation Safety Agency already mentioned.
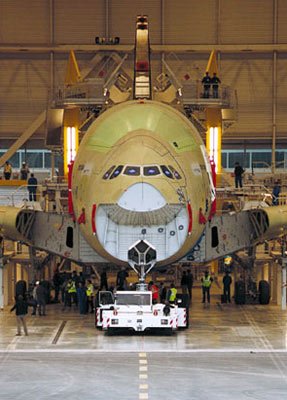
Assembly of the Airbus A380
But before a type certificate is issued, and even before the production of the aircraft begins, the aeronautical authority must validate the design from the point of view of compliance with the airworthiness standards [18] established by those bodies.
The process for type certification involves an extensive program of tests, among which are:
Structural and fatigue tests of material.
Flight tests.
Evacuation tests of the passenger cabin in case of emergency
The objective of this process is to verify that the design of the airplane conforms to the regulations in force, which complies with the flight characteristics included in the design, as well as the requirements regarding the resistance of materials, the structure, engines or on-board equipment.
The testing program:
A test program requires the construction of several prototypes. Each of them will be dedicated to cover specific sections of the program. If a prototype - or several - were not available and the series aircraft were built directly, it is very likely that there were problems, some unpredictable, which would lead to numerous modifications of the series aircraft, an increase in the cost of the project and risks for passengers. For this reason, it is necessary to carry out several thousand flight hours of prototype tests or prototypes to verify and adjust the operating data calculated during the design process, as well as the modifications that are introduced in the model. After this phase, the final design of the series aircraft, the production process and the certification tests required by the aeronautical authority are reached.
A part of the tests is performed on the ground without the need to take off, such as the bending of the wings and fatigue of the material.
Structural fatigue tests:
During the structural and fatigue tests to which an airplane is subjected, studies are carried out to verify, among others, the maximum loads that it will be able to withstand during take-off, in flight and during landing, as well as the forces and deformations that the structure is capable of supporting. The design philosophy regarding structural fatigue must ensure that during the operational life of the aircraft and any circumstance that it can find, the possible cracks that may arise do not reach a critical size without being detected. So, during the certification tests special attention is paid to structural behavior subjecting the aircraft to fatigue conditions.
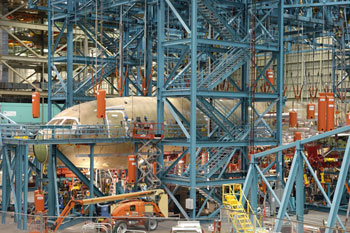
Tests of resistance of the wings in a Boeing 787
The fatigue tests to which the plane's wing is subjected are very striking due to their spectacular nature, which mimic the flight cycles to which they are going to be exposed - detachment, flight and landing, as well as other possible circumstances such as turbulence or forced landings - to ensure that any cracks that are created do not reach a critical size.
In this test, mechanical actuators subject the wing to loading and unloading successively during a high number of cycles, which reaches a value close to that expected during its operational life.
Eventually, cracks occur on purpose and he continues to flex up and down to study his behavior. The speed of propagation is also verified in order to establish the appropriate inspection intervals, which guarantee their detection during the operational life of the aircraft.
With the results of the tests, manufacturers develop crack detection mechanisms that ensure that they never jeopardize the safety of the aircraft.
The test flight:
The test flight is intended to verify the general qualities of aircraft handling, their operational characteristics and the operation of the systems, both in normal operation and in case of failures and extreme conditions. This type of flight is carried out by expert test pilots.
When an airplane leaves the hangar where it has been assembled to make its first flight, it will be the first of a series within the test program that will be combined with other activities of experimentation and analysis on the ground. As already stated, these tests must show that the aircraft complies with the regulations in order to be certified and declared fit for the operation. Throughout the process, the data that is obtained is transferred to the design department to make the necessary corrections and improvements.
Test conditions:
The following tests are carried out on the airplane, among others: It is exposed to adverse weather conditions, which leads to extreme temperatures that can range from 45 degrees below zero to 50 degrees above zero, during which it is verified the correct operation of essential systems such as: motors, brakes and navigation, among others. And to fly through storms to check how the airplane behaves under conditions of strong turbulence, negative forces "g", and the operation of anti-ice systems.
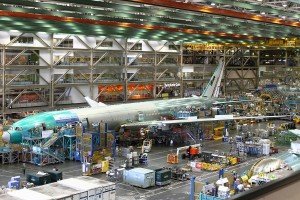
It is also subjected to operations on tracks at high altitude, such as the one at La Paz Airport, in Bolivia, at an altitude of 4,000 meters.
Another test is to make the plane land on a wet runway to check its braking capacity. And another with strong crosswind, in which its maneuverability and stability is verified. The high-capacity aircraft that are manufactured today are capable of landing in crosswind conditions of up to 100 km / h. And they must do so with a maximum deviation from the runway axis of just over five meters. Because of the danger to the engines of ingesting water, the plane is subjected to landings in flooded runways to verify that the aerodynamic design of the airplane , as well as that of the landing gear, prevent the entry of water into the engines.
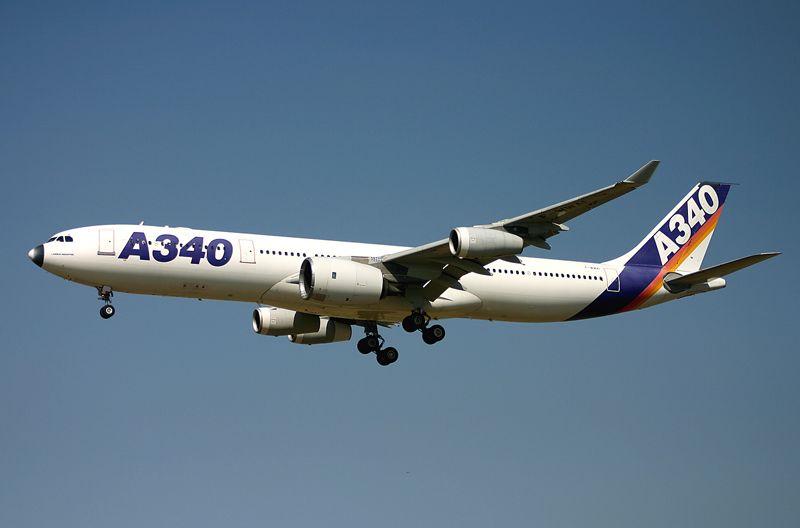
Airbus a340 testing an Airbus A380 engine in flight.
There is also the aborted takeoff test. This test consists of checking the response of the aircraft with the maximum weight at takeoff, given the possibility of having to perform an emergency braking in case the takeoff is aborted just before reaching the decision speed V1. For this, the prototype is installed a brake system manipulated so that its operating conditions correspond to those that would have 90% of the maximum allowed wear and the plane is subjected to maximum braking.
The aim of the test is to verify that, after maximum braking, the braking system does not catch fire, nor does it cause serious damage to the aircraft.
Evacuation tests in emergency:
Another important test block includes those related to the evacuation of the passenger cabin in case of emergency. To overcome this test, the aircraft must be completely evacuated by passengers and crew in less than 90 seconds - time set in the rules - in the dark of night, with half of the exits blocked, and with luggage and other obstacles placed in the corridors and escape routes. The interior of the aircraft can only be illuminated with emergency lighting [19].
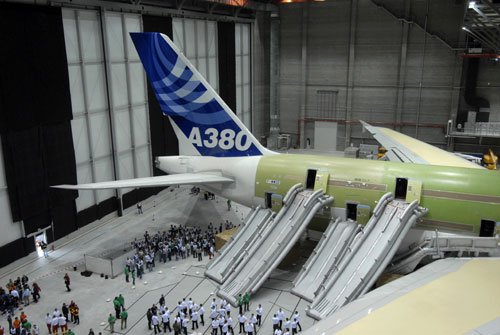
Route evaluation flight:
Another test to which the airplane is subjected in order to verify the functionality and reliability of the conditions for the passenger, is the one that simulates a line flight with passage -generally employees of the manufacturer- representative of the commercial characteristics objective and with a time of flight similar to what will then be done in a normal operation. In it, the correct functioning of all the systems of the plane is checked, paying special attention to the aspects of the passenger cabin, such as ventilation systems, temperature, noise levels, the operation of the toilets, etc. This gives the opportunity to correct possible deficiencies and make improvements.
Infrastructure compatibility:
Finally, it should be noted that in the event that the new aircraft is somehow an innovation, as was the Boeing 747 and currently the Airbus 380, tests are carried out to verify its compatibility with airport infrastructures. During these tests, the new airplanes carry out visits to a series of airports around the world, which verify their compatibility with the services offered by airports such as: handling, refueling, fingers, etc.
All these tests can come to assume, in the case of the latest generation long-haul aircraft, more than 2,400 flight hours over more than 700 flights.
On the other hand, once the aircraft is already operating with an airline, if it detects any deficiency, it immediately informs the manufacturing company, which will be in charge of notifying the rest of the airlines that have aircraft in their fleet. model. At the same time, an analysis process will begin to find out the cause of the deficiency, find a solution and, finally, disseminate it to all of its clients for correction.
We take care of your plane, we take care of you:
A modern passenger transport plane is a very complex and sophisticated machine that requires careful manufacture and an exquisite maintenance to guarantee its perfect operation. These are the reasons that have led to the high levels of security achieved by current aviation and its subsequent success. Therefore, as there are many things that can fail, make no mistake, before an aircraft is considered available to perform its mission, a large group of specialized professionals must have worked on land accumulating in it many hours of work in order to guarantee its correct functioning [20].
This work is based on the maintenance plans that each manufacturer makes for the models of aircraft that they manufacture, which are incorporated into the technical manuals, which specify in detail how maintenance operations should be carried out by the airlines. Along with the maintenance program, manufacturers also provide airlines with a Minimum Equipment List (MEL), which includes, among other things, the minimum conditions that an aircraft must meet in order to operate. In addition, each plane has a "deferred book" in which the maximum time a repair can take is delayed when the anomaly is not considered important. Then, airlines can introduce more restrictions to these lists, but never less. Maintenance plan, technical manual, MEL and deferred book must be approved by the aeronautical authority of each country, which in the Spanish case is the General Directorate of Civil Aviation.
There are two types of maintenance: scheduled and unscheduled.
The purpose of scheduled maintenance is to maintain the aircraft in optimum flight conditions based on a preventive programming that must conform to the specifications given by the manufacturer, to use the information provided by other airlines that use the same aircraft and for the technical circulars and safety directives issued by the State Aviation Safety Agency. It is divided into three categories, which cover inspections whose intervals and tasks are progressively longer: on-line maintenance, minor maintenance and major maintenance.
Online maintenance:
It is usually carried out in the same parking lot and is composed of three inspections: daily, transit and revision.
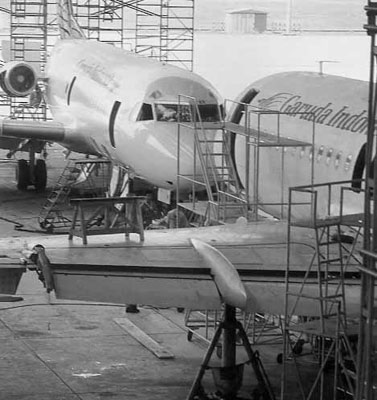
Daily:
Before the departure of the first flight of the day, a maintenance technician carries out a review in the same parking lot to check the general condition of the aircraft: possible fuselage and wing damage that may have occurred during the time it has been parked, as well as of indicators, registers, connectors, etc., of all the services that have been connected to the plane since arriving at the airport. State of wheels and brakes, extension of the dampers of the landing gear, check of oil levels, hydraulic, oxygen pressure of the auxiliary system and review of the on-board emergency equipment.
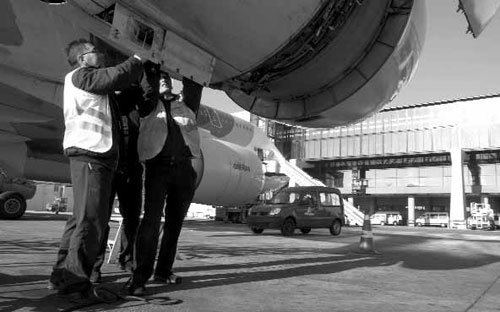
Transit:
Before each flight and as close as possible to the exit, an external inspection must be carried out in order to check again the general condition of the aircraft: possible damage to the fuselage, landing gear and wings, which may have occurred during the flight or during the stopover. It is also verified that the registers and connectors of all the services that have been connected to the airplane on the scale, such as fuel, wastewater, electricity, etc., are correct for the flight.
Review:
Every hundred hours of flight, all aspects related to safety are checked, possible anomalies are corrected and a complete set-up is made to the aircraft.
Minor maintenance:
It consists of an inspection around the plane, the review of some specific elements and the correction of those who need it. It consists of three inspections:
Revision A: includes a general inspection of systems, components and structure, both from inside and outside, to verify its status.
Revision B: of greater importance than the previous one, in it the safety of systems, components and structure is checked, the set-up is made to the airplane and the elements that require it are corrected.
Revision C: it is a complete and extensive inspection, by areas, of the interior and exterior of the aircraft, including the systems, the facilities and the visible structure.
Major maintenance:
This is Review D, also known in professional slang as "Great stop" and, since it is the most complete and meticulous that can be done to an aircraft that can be used for several months, in it They include works such as the complete pickling of exterior paint [21], the disassembly and revision of engines, landing gear, flight control surfaces such as rudders, ailerons or flaps, ramps, seats, hydraulic systems, window panes and all interior cladding panels, both on the walls and the floor, not forgetting hundreds of kilometers of cable. Then, everything is assembled and painted. And before the plane returns to transport passengers, a test flight will be conducted by specialized pilots and technicians, who exhaustively and according to the manufacturer's standards, verify that the aircraft meets the required specifications. It's as if the plane had just left the factory with zero hours of flight. Like new
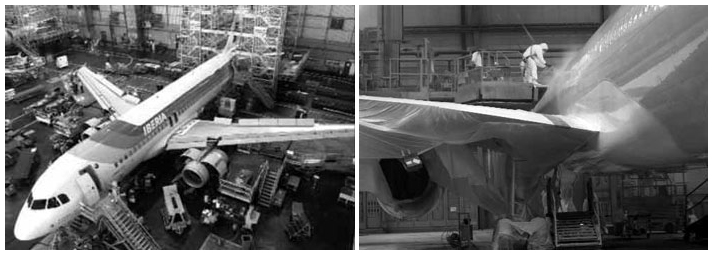
"Great stop" of an Iberia Airbus 320 and subsequent painting phase
This type of maintenance in the case of an Airbus 340 is carried out every 10 years, being able to be in this phase for several months during which around sixty thousand hours of work are used. The cost of the process can be between 4 and 5 million euros, of which 15 to 20 percent are used in the purchase of spare parts [22].
It could be said, in short, that in the history of an airplane there should be more hours of maintenance than of flight.
To conclude, in Spain, the State Aviation Safety Agency is the body responsible for supervising the maintenance program and conducting periodic audits to verify that there are no deviations from the established maintenance procedures. Also, once it has been verified that they have been carried out After all the established revisions, it is the person who must renew the airworthiness certificate of each plane every year.
FOOTNOTES:
[16] The weight, is the measure of the force of attraction that exerts the terrestrial gravity on a body. If the force of attraction is made with an acceleration of 9.8 m / s2, it is said that the force is 1g and will be equal to the weight of the body.
If the acceleration were double, the force would be 2g and its weight would be double and so on.
Examples of force g:
- When detecting an acceleration equivalent to 3g, the airbags of the cars are activated.
- A fighter in a turn can produce 7g.
- A Formula 1 can produce in a braking 5g and 3g laterals in the curves.
[17] The type certification of a new design is a responsibility that corresponds to the aeronautical authority of the country where the company that designs and manufactures the aircraft is located. The aeronautical authorities of those countries where such aircraft are to be registered, can choose to accept the type certificate issued, or perform a technical verification or validation process, after which they issue their own type certificate.
[18] Airworthiness is defined as the situation of an aircraft that denotes the best technical condition to interact in the air environment safely.
[19] If any of the doors is inoperative, the airplane's capacity for passage must be reduced.
[20] All personnel performing maintenance tasks must be accredited as a Technical Specialist in Aircraft Maintenance, TMA, and all work must be supervised by a certifier, who offers the guarantee that the work has been done in accordance with the standards established.
[21] The reason for stripping the plane of the paint is to check the panels of the fuselage and the rivets that join them. Once the fuselage, the wings and the control surfaces have been checked, they are inspected with X-rays to check if cracks exist, the necessary elements are replaced, everything is assembled again and repainted. The exterior of an Airbus 340 requires about one ton of paint.
[22] It must be verified that damaged parts and those that have completed their useful life cycle do not re-enter the aircraft repair circuit. This is achieved with a rigorous control that can even verify the physical destruction of the replaced parts.
##http://direcaereomecanismos.blogspot.com/2016/05/el-avion-disenos-fabricacion.html
##http://www.demagcranes.es/Industrias/Construccion-y-mantenimiento-de-aviones
##http://avionesdelinea.blogspot.com/p/airbus-a330-200.html
##http://bibing.us.es/proyectos/abreproy/4922/fichero/5_FASE+DE+DESARROLLO.pdf
I do not know much about countries other than U.S., but I do know the logs must be very detailed. I've known two Navy Aviation Mechanics (Mechs) and the maintenance is so vital. As you mentioned in your post, the plane must endure fatigue stress and then after X amount of flight hours more testing is done. One man told me they would get down with a magnifying glass to find stress cracks.
Recently, I heard an advertisement stating that airline mechanics must get their hearing checked frequently. Why? So they can determine any difference in engine and other sound factors. Great post.
If because through the sound of the engine, can cause hearing difficulties and may be deaf so recommends earplugs as protection, thanks for dedicating read my post
If you want reliable aircraft make sure you have all maintenance bases covered from adhesives, to paints, aircraft tapes to sealants.
This website is so cool! I keep coming back because I learn a bunch of new stuff every time. It's easy to understand, and that makes it even better more