Plant Layout - An Insight into structuring of Plant Equipment
Greetings Steemians. It’s great writing again.
I noted in my previous post on plant siting that there will be a sequel to that article and today is when we treat it. If you could remember, I mentioned that both articles could actually stand independent of one another but I have decided to make them into a series because of a reason you will understand soon.
Today we will be looking at Plant Layout, which is simply the arrangement of the equipment contained in any industry. A careful consideration will show that having properly sited a plant and completed the construction, the next phase is to install the production equipment.
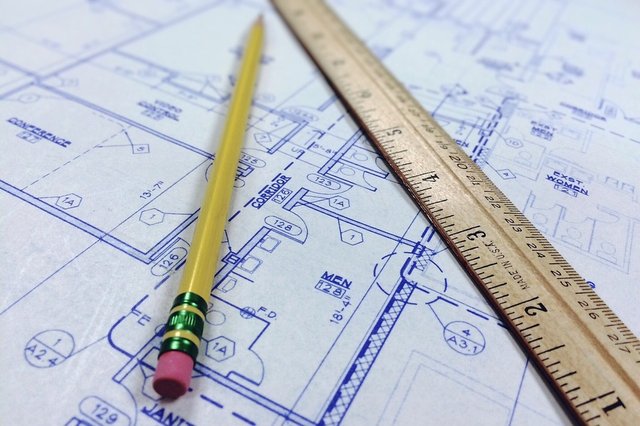
Plant layout is the physical arrangement of all plant facilities. A definition I like is that given by Kumar and Suresh (2008) which is: “the configuration of departments, work centres, and equipment in the conversion process”. The implication of this definition is that plant layout, encompasses the arrangement of all that can be found in any industrial outfit. However, we will focus on the production function in this course.
Certainly, there is more than a big deal in equipping a plant as there are goals that should be met by the chosen layout albeit each layout has what it can offer and what it cannot. Hence, there’s need for the organization to have an understanding of the scope of the potential layout and then check if this will fit their needs.
Whichever the case may be, there are certain features any production venture will desire that a layout offers.
Let’s discuss them
To begin with, we know raw material resources are not the only resources needed in an industrial setup, human resources and machinery are other resources that are needed. It is essential that these resources are properly integrated into a whole, allowing for efficiency and effectiveness. It’s no doubt a plant layout determines how easy it will be for these resources to work together and thus having an optimum layout will go a long way in ensuring this.
Space utilization is another consideration. Plant facilities must be installed such that it ensures an optimum space utilization. That is, the work area must allow for movement and at the same time, no area is left unnecessarily fallow. Another point worthy of note in this regard is that the optimum space utilization requirement does not encompass only the horizontal or flow space, but also the vertical space. Consequently, we say “Optimum cubic space” utilization is required.
Furthermore, we want to manufacture a product such that each process that we need to carry out on it is done at once, without the need to revisit a previous step. That is the structure of the plant equipment should be such that allows the work to move forward toward the end stage of production. While moving into different stages of manufacturing, we also want to travel the fewest distance between each stage as this would buy us more time which we know is money.
Aside, helping the organization to achieve its objective, we need to consider the human element in the production outfit. Their security and satisfaction must be guaranteed as it is only through this there can be continuity in the organization.
Does it look like I have been twisting things up here? Let’s go into the main discussion to have a better inkling.
So, how do we structure plant equipment?
Like the proper siting of an industry, a proper plant layout is essential to aid the operation of any plant. A poor plant layout leads to greater manufacturing cost and production losses. This is due to the fact that material travel and hence material handling cost will increase.
A saying in my native language loosely translates thus: “there are numerous entrance into a market”. In the case of arranging plant equipment and hence plant layout, there are many ways in which it can be done depending on the need of such production venture. Let’s look at them. I will begin with Product layout.

Product Layout
In a product layout, a product is dedicated a whole section and there are several of such section within the organization. The equipment in each section is arranged in the sequence by which they perform an operation of the concerned product.
Let’s give a loose illustration
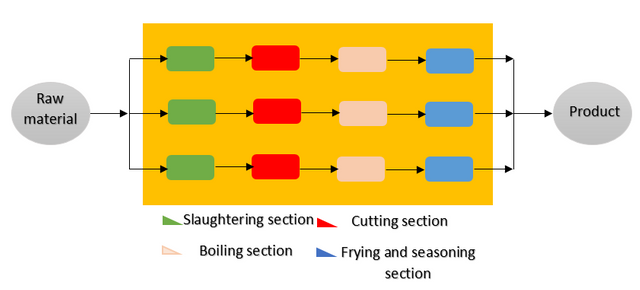.png)
Imagine in a meat processing industry that offers fried meat as their finished product. Let’s assume they provide three varieties of meat – Chicken, Beef, and Chevon (Goat meat). Take the processing of each to be in a sequence involving four operations – Slaughtering; cutting; boiling; Frying and seasoning.
If such industry utilizes a product layout, each product (meat type), will have a dedicated department for it, with each operation to be done having a section with the department and all following the stated sequence. That is, Chicken will have a dedicated department having a killing section, cutting section, boiling section and frying and seasoning section
in that order. Same goes for all the other products.
Moving on, with this type of layout, there is better utilization of space and the overall manufacturing time is reduced as there will be no delay between each operation, that is, little or no handling. Furthermore, it allows for better use of resources and gives a better guarantee of delivery to the consumers. The possibility of utilizing gravity and power conveyors for the handling of materials is also afforded.
On the other hand, the product layout has some shortcomings. An obvious one is that which has to do with a breakdown of any of the machine along the production line. In such case, the shutdown of machines downstream of the faulty machine results and hence, the whole production line will have to go down. Imagine in the illustration above, when the killing machine breakdown, subsequent operations are not possible since they depend on it.
Furthermore, since the production line is dedicated to a given product, a change in the product amounts to a change in the production facilities in that area. Adding more machines to the production line alters the required operations that are to be carried out on a product and thus the possibility of this is nil. In addition, in any case, if reduction in the standard production volume occurs, the cost of production increases – remember this type of layout thrives on volume.

Process Layout
In a process plant layout, “similarity of function” is the key phrase. This is due to the fact that all equipment are grouped according to the function they carry out with equipment carrying the same function placed in the same location. Each group can be viewed as a department within the organization, carrying out the same process, hence the name Process layout.
This type of layout is suitable for a venture that manufactures products in batches. Furthermore, such layout is suitable when the quantity of product manufactured is low. An example is a machine shop where the product variety is high but production volume is low.
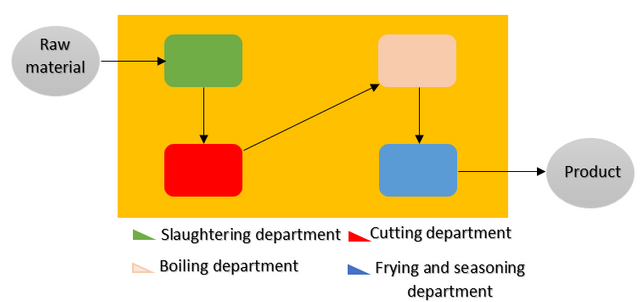.png)
Take the previous illustration again. If such industry uses a process layout, there will be for departments viz: Killing department, cutting department, boiling department and frying and seasoning department. All killing operation will have to be referred to the killing department regardless of the kind of meat to be made.
Unlike in the product layout, no single product is dedicated a single operating area and as a result, the number of machines required is not as much as in product layout. The expansion of the production facility is easy since we can easily add a machine to each section without altering the operating sequence – hence flexibility. Also, the breakdown of a machine does not affect the other machines and thus there’s not production loss in this regard.
Well as you may have guessed, there are shortcoming to this type of layout as well.
The aim of any production industry is to minimize material handling as it study has shown that a substantial portion of the production time is taken by material handling. Unfortunately, the process layout has little or nothing to offer in this regard as there is need to carry materials from one section to another section for other operation to be carried out on them.
Backtracking is another case. That is, revisiting a previous operation or section. Also, any industry will want to use the equipment purchased for production to its optimum capacity, that efficiency for you. The adoption of a process layout gives any venture the ability to utilize their production facilities to the fullest making sure that efficiency is always present.
In addition to the above, manufacturing time is increased due to some factor like not being able to mechanize material handling. This result in a lower turnover of inventory and thus a high process inventory.

Fixed Position Layout
In the above discussed layouts, you will observe that in either case, product in the process moves from one production unit to the other. That is the work moves from one section to another section until it becomes the finished product.
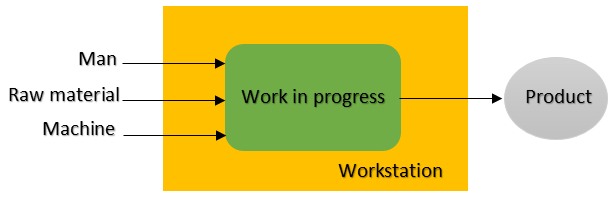.png)
However, in the case of a fixed position layout, the reverse is the case. Here the work sits in a fixed location and all the resources needed are brought to it – Men, Materials, and Machines. Such is employed when the finished product is that which is bulky and heavy. Example of such kind of layout is found in Ship and Aircraft making industries. Other examples are construction works where all resources must be taken to the place where the finished construction (e.g. Dams and bridges) is to be situated. Funny enough, I have seen in a TV show where a house is built elsewhere and transported to the owners land for installation.
The transport of resources to the work area gives this layout type flexibility as any required resource can be brought in to meet any changes in the product. However, fixed layout poses the problem of space within the work area as there is a high tendency of the work area becoming crowded and in fact, this could cause some material handling issues.

Combination Layout
So if you have been wondering if it is possible to have all the discussed layouts in a single industry so that each can complement the others, then here we are – the combination layout. As you must have guessed, combination layout is the utilization of any combination of the above discussed layouts and the obvious advantage is to have a layout that taps into each singly existing layouts.

Conclusion
The aim of any production venture is to make products to satisfy the need of a group of people. Every of such venture thrives to improve their customer’s satisfaction by stepping up the quality of their product and at the same time maintaining productivity in other to earn a justifiable return on their investment.
Productivity equals production efficiency, which is how much output an organization derives from the input. There are numerous means by which an organization can achieve this goal and utilizing the best layout can be the best way to start. As noted, there’s no single layout with all the needed features. Thus an organization must decide which best assist them in achieving their goal.

References
- Ismaila, S. O. Production Management. Federal University of Agriculture, Abeokuta.
- Kumar, S. A and Suresh, N. Production and Operations Management (Second Edition).
- Wikipedia | Plant Layout study
- What Is Sixsigma.Net | Plant Layout study
- Your Article Library | Industrial Plant Layout: Meaning, Definition, Need and Importance
- Business Management Ideas | Plant Layout: Meaning, Factors, and Tools
If you write STEM (Science, Technology, Engineering, and Mathematics) related posts, consider joining #steemSTEM on steemit chat or discord here. If you are from Nigeria, you may want to include the #stemng tag in your post. You can visit this blog by @stemng for more details.
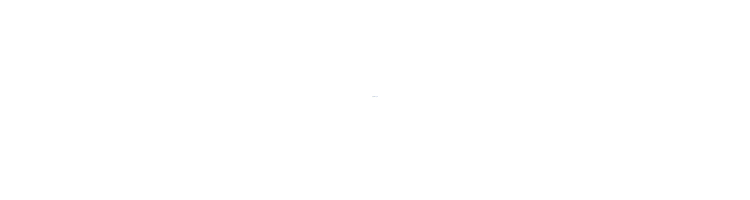
Thanks for this informative post. At least after plant sitting you do layout. I think is the same for building houses too now. Thanks boss for the informative post. @temitayo-pelumi
My pleasure.
Hello! I find your post valuable for the wafrica community! Thanks for the great post! @wafrica is now following you! ALWAYs follow @wafrica and use the wafrica tag!
Great post boss
Having a plant layout is as important as building the plant itself. Hence there must be a thorough plan before starting out to build
I couldn't agree more. Thanks!
Definitely, layout should be the next step after properly siting a location. Thanks for further providing us with a guide. People with plans of setting us a plant can actually learn a ot from here. Nice creativity with the images..Made it more understandable(do attribute it)
Oh... thanks for drawing my attention to the images. I don't know why I was carried away when I posted it. I guess I was kinda tired. Thanks for dropping by man.
You're welcomed. Always a pleasure
Good Post. It's good thing to have a good layout for every thing we have plans on.
Thanks.
Interesting read. I had never though about the fact that there could be particular layout methods incorporated in a plants
Kudos bro
I'm glad you gained something man. It's good to have you drop by.
Beautifully written....Thanks for sharing this
Kudos!
Thanks for the kind compliment. It's my pleasure sharing.
Hi @temitayo-pelumi!
Your post was upvoted by utopian.io in cooperation with steemstem - supporting knowledge, innovation and technological advancement on the Steem Blockchain.
Contribute to Open Source with utopian.io
Learn how to contribute on our website and join the new open source economy.
Want to chat? Join the Utopian Community on Discord https://discord.gg/h52nFrV
Thanks for the support. The SteemSTEM community appreciates it.
can you tell me where your plant is?
Judging by your posts, i feel you have one
If he has any plants, it's the beans in his backyard.
lol at least its still a plant
😂😂😂... Its shuku agbado that is there.. 🤣🤣
🤣🤣🤣🤣
In all successful endeavours in life, planning is one of the most essential ingredients
Great post buddy!
A popular saying goes thus: "a man who fails to plan, plans to fail".
It's good to have you here man. I hope to see you often.